Arpocore™ Aramid Powder
Aramid is the collective name of an aryl peptide polymer with remarkable properties. The material exhibits unique characteristics including strength, wear resistance, flame retardancy and anti-slip. It decomposes at 525°C and has no melting point. For coating and flooring applications Arpocore™ can be used to impart anti-slip and friction properties along with improved wear resistance. It is easy to use, and the resulting product is easy to pigment to the desired colour.
Characteristics
- Excellent wear resistance
- Fire retardance
- High friction control
- Good resistance against organic solvents
- Not conductive (electricity)
- No melting point, decomposes above 500˚C
- Temperature resistance: continuous up to 250˚C, brief up to 500˚C
- Density: 1.45
- Bulk density as powder: 300- 500kg/m3
- Factor 5-8 higher tensile strength as steel (weight basis)
- Excellent insulating properties (heat) minimises heat absorption
- Low elongation properties (typically 3.5% at break)
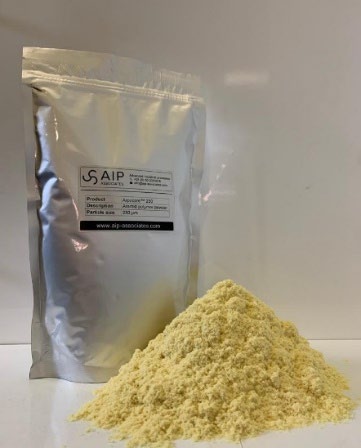
Standard Grades
Description
Arpocore™ 125
Arpocore™ 125 is our finest grade with particle size up to 125μm. This grade can for example be applied in engineering plastics for wear resistance, extreme friction control, noise reduction and more.
Arpocore™ 250
Arpocore™ 250 is also a fine grade with particle size up to 250μm. This grade can for example be applied in coatings to increase wear resistance and anti-slip properties of the final product.
Arpocore™ 1000
Arpocore™ 1000 is a coarse form with particle size up to 1000μm. This grade can for example also be applied in coatings and further increases the wear resistance and anti-slip properties. (coarse circumstances).
- Tank roofs
- (Industrial) floors and workshops
- Ship decks (pleasure/yachting, commercial/industrial and naval)
- Offshore platforms
- Bridges, roads, car parks and garages
- Gyms, saunas, and swimming pools
- Platforms, scaffolding, stairs, galleries, balconies, and roofs
- Any other coating applications where (amongst others) pigment/colour adaptation, friction control, cold temperatures and heat accumulation play an important role
- Arpocore™ can be applied for controlled/improved anti-slip properties, it offers friction control in different particle sizes
- The wear resistance of Arpocore™ is better than minerals, sand, and stony materials. They become “loose” quickly due to low adherence to the coating, whereas Arpocore™ becomes integral to the coating.
- Arpocore™ serves as a fire retarding agent
- Arpocore™ does not sag to the bottom quickly, allowing for adding/mixing of the product either in the factory or on-site.
- Arpocore™ is compatible with colour/pigments and resins (“adopting” the colours used in the coating and improving adhesion to the resin).
- As mentioned, Arpocore™ itself is highly wear resistant. This, combined with its characteristic to “become part of the coating” extends the lifetime of the coating, especially when compared to other minerals and additives
- Arpocore™ has no heat absorption/storage compared to fillers such as sand, korund and such like, and can therefore even function as isolation (important for e.g. leisure ship decks, but also tank roofs).
- By mixing Arpocore™ into the coating, the application of a friction increasing agent by a separate action is not required. This saves both material and man hour costs.
- Arpocore™ added in coatings gives the coating more “body” (structure), allowing for more effective/equal covering of the surface
- Arpocore™ does not contain halogens
- Arpocore™ is spark free and therefore ideally applied in hangars, oil/chemical tankers, tank roofs, chemical factories, etc
- On a steel substrate, Arpocore™ will not accelerate corrosion. This, compared to stony materials creating “weak” spots as water/moisture migrates through the cavities due to the incompatibility of the inorganic stony material with the organic coating
- Arpocore™ is very light compared to e.g. mineral fillers/additives and only a relatively small weight/amount of powder is required to cause a significant friction increase. Quantities of 10-65 grams per litre are used, which is a factor 2 to 10 less than other materials.
To arrange samples and further information please contact us
Tel: +44 (0)1530 561957
Email: [email protected]
To the best of our knowledge, the information contained herein is accurate and reliable as of the date of publication; however, we do not assume any liability whatsoever for the accuracy and completeness of the above information. Plastribution Speciality Chemicals makes no warranties which extend beyond the description contained herein. It is the customers’ responsibility to inspect and to test our products in order to satisfy themselves as to the suitability of the products to their particular purpose. The customers are responsible for the appropriate, safe and legal use, processing and handling our products.